What the press reports about us
Milling at the limit – earned when it rains chips
Most hoggers lose courage when they chase their tools through cast iron and steel with 80 percent of the power reserve. A cast operator in Ennepetal sees things somewhat differently: “Money is earned when we make full use of the tool performance. We have found that there are often more reserves in the tools than the manufacturer dares to state in his data sheets. The Perspective for this, however, is a sufficiently stable machine and the workpieces suitable for this test of courage.
Well, both apply in this case. The company “e-form”, Ennepetaler Formkästen, produces among other things flasks, cooling car and pattern plate carriers for foundries, as well as contract casting processing for large parts. Almost all foundries worldwide are supplied with flasks and accessories for manual moulding or for fully automatic moulding plants. Close technical cooperation exists with Heinrich Wagner Sinto, the world’s largest foundry plant manufacturer. In recent years, e-form has established itself as the undisputed market leader on the international market for box-bound moulding plants. Flasks are available cast or welded for each stage of mechanical stress in dimensions from 400 x 400 to 4,000 x 4,000 mm, in individual cases even up to 6,000 mm.
The problem with the machining of flasks and other cast parts made of GG20 to GGG50 is multi-layered: cast skin with sand inclusions, blowholes, constantly changing oversizes and cutting conditions, hard spots in the casting require a high tolerance range of the milling cutters used. The tools are subjected to particularly tough tests during the overhaul of old bottles with hard cast overflows. These flasks, used in tens or hundreds of thousands of casting cycles, partially repair-welded, are “glass hard”. The company, which was founded on April 1, 1920, has been equipped with between 50 and 500 upper and lower box mould pairs each around the globe via moulding plants since 1985. The unit weights vary between 100 and 5000kg per box half. 6,000 tons of cast iron are processed on average annually in the 20-man operation.
“My machines, two Zayer portals and a Zayer bed milling machine with up to 45 kW at the spindle, cost about four marks per minute. So if I’m 30 percent faster, that’s 80 marks per hour less cost, and I can sell the higher productivity again. Even if competition plates should be two marks cheaper, then that’s still no use to me. He who still does the math today, does the math wrong. ” The 30 percent higher productivity is the result of longer service life and less downtime, higher process reliability and higher possible feed rates. Karl-Heinz Tielmann, Product Manager Milling at Iscar, provides the reason for the performance of the Iscar plates: “The IC 910 plate used has high bonding strength of the normal-grained substrate and the resulting high cutting edge hardness is single-layer PVD coated with TiAIN. Above all, the good adhesion between the base substrate and the coating is decisive. The positive cut of the plate, in combination with the radially and axially positively adjusted carrier tool and the helix geometry, produce a light and soft cut”. And Harald Wolf, owner of Ischebeck Zerspanungstechnik and Iscar authorised dealer in Ennepetal adds: “Due to the quality, the cutting edge wears predictably without breaking and without damaging the carrier tool”. Werner Bühren: “There are considerable reserves in the tool. In some cases we achieve machine performance data just below the performance limit of the Zayer with 45kW with the 63 face/corner milling machines, without the tool being damaged – that means something! And the same performance profile is achieved by machining with the IC 328 plate. “
However, the parameters cutting speed and feed per tooth are not intended to provide information and make competitors aware of them. Let everyone find out for themselves. Only this much can be said: The approximately 22m travel in the machining of the contact surfaces of the top and bottom box and the guideways with an average machining width of 40 mm, including the eyes for the guides, took about half an hour in one set-up during the observed machining. One cutter assembly is sufficient for this rough application for about 45 to 50m milling distance. But let me tell you a trick: A newly equipped milling cutter is always “gently retracted” until the cutting edges have grinded into each other in the µm range (tip picker) and all plates are evenly engaged – about one to two meters – and then it can work at full power. By the way: With every new approach to the casting skin, the gas is taken back for a few centimetres – this brings additional service life.
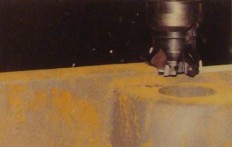
Through hard zones on the centering eye and with 10mm cutting depth. Earned when it rains chips.
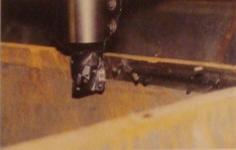
The inside contour is machined with the end mill. The cutting depth varies between 2 and 12mm.
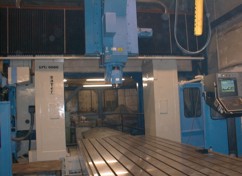
With 45kW at the spindle of the Zayer KPU 4000 sufficient robust reserves for machining with at times 130 percent of the milling capacity according to the data sheet.
Report from the IHK issue March 2018
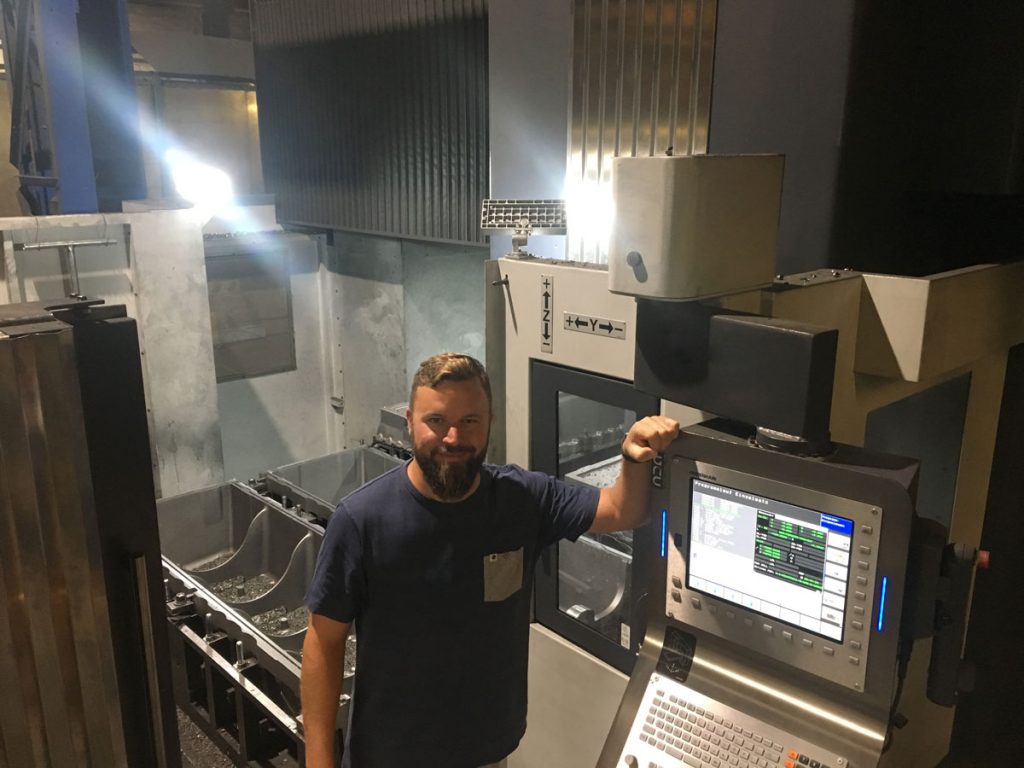
FRANK LEWANDOWSKI TOOK OVER ENNEPETALER FORMKÄSTEN BÜHREN GMBH
After 13 years, he owned the company
There can hardly be any better conditions for the takeover of a company in the course of an age succession. After his training as a cutting mechanic specializing in milling technology, subsequent civilian service and a stay abroad, Frank Lewandowski worked as a programmer for CNC milling programs for Ennepetaler Formkästen Bühren GmbH from 2001. As early as 2008, he headed production there and ensured that the company abbreviation E-Form became a technical term in foundry circles through customer-specific problem solutions. One and a half years later he was appointed management assistant and was involved in key corporate decisions in this function. “I know all facets of the company,” says Lewandowski, whose father had been an employed managing director of the company for 27 years.
When the company owner decided to sell the company in 2014 for reasons of age, because there was no successor in the family, Frank Lewandowski did not hesitate. However, financing the seven-figure purchase price initially proved problematic: a first credit institution revised its loan commitment. Ultimately, a second bank and Bürgschaftsbank NRW. The former offered Lewandowski a tailor-made financing also with public funds, the latter went into the commitment for a seven-digit loan almost with the surety amount. “Everything worked out beautifully, but without a guarantee the financing would have become very difficult, since I understandably did not have the necessary own funds at that time and could not provide any securities”, sayd the 39-year-old company boss today.
Four years ago Lewandowski took over a long-established company: Founded in 1920, Ennepetaler Formkästen Bühren GmbH (E-Form) produces mould boxes for the foundry industry, initially riveted, later in welded form and developed into the market leader in Europe in the 1980s with the introduction and conversion to CNC production. The range of services includes the design and manufacture of welded flasks for manual and machine moulding shops as well as flasks for high-density moulds for fully automatic moulding lines.
A flask usually consists of an upper and lower part. A sand mould with sometimes complex structures is pressed into both parts. These flasks parts are precisely superimposed on the sand side and closed. Liquid metal is poured into the sand through an opening on the top of the flask. Once the iron has solidified, the cast product can be removed from the mould by destroying the sand mould: for example engine blocks, gearbox housings, counterweights for forklifts, pump housings, axles with high unit weights, but also lighter parts such as brake discs, engine manifolds, catalytic converters, even grave decorations or water taps. Castings are used in all industrial sectors, but also in private households.
Currently, large square flasks weighing more than two tons are being produced in Ennepetal for a fully automatic moulding plant in the USA. The main field of activity is in Europe, but foundries are also supplied worldwide. Another product in which the Ennepetal company specializes is oil pans. They are up to 2 meters long, 70 centimeters wide and 40 centimeters high. The cast-iron tanks weigh around 400 kilograms and form the end of 16-cylinder diesel engines used in ships, power generators, commercial and construction vehicles and biogas plants. Together with the flaskes, they are processed, packaged and prepared for shipment by truck and ship on a production area of around 3,000 square metres.
However, these two production legs of the Ennepetal company are not enough to secure jobs for Frank Lewandowski. Mechanical processing of large parts, weighing up to seven tons, has been another mainstay of Ennepetaler Formkästen Bühren GmbH for some time. In the size of six by three meters, metal parts can be machined.
In December last year, the 39-year-old put a new five-axis portal milling machine into operation to ensure delivery capability. The plant, which costs one million euros, has a processing area of 4. 50 by 2. 20 metres. Four oil pans can be machined fully automatically at the same time – with a precision of a thousandth of a millimetre.
“Speed and precision are expected and appreciated by our customers. For them, rework costs time and money,” says Frank Lewandowski. In order to maintain the satisfaction of its customers, the production currently works in two shifts with 22 employees. With sales of 5. 5 million euros last year, the company again achieved a positive result.